One of the key responsibilities of a Reliability Engineer is to implement a reliability plan identifying inspection and value-added preventive maintenance tasks as well as replacement planning. The reliability plan needs to consider longer term production schedules, planned outages, as well as the risks allowed.
To plan preventive maintenance tasks and replacement planning for turnarounds you can consult OEM operational lifetime information and maintenance tasks as well as failure databases. In addition the company might have in-house experience for selected assets and components. There are several databases that exist that have Mean Time To Failure (MTTF) and Mean Time Between Failure (MTBF) data for industrial assets. These databases can support you in determining the Remaining Useful Lifetime (RUL) of your actuators and valves. But there is a caveat in using these as they do not take into account your specific operating conditions and the level of maintenance and repairs you have given your valves and actuators.
Turnaround projects are massive projects that must ensure the reliability and safety of the plant for the next years. Every day the plant is not producing during a turnaround, money is lost. Therefore, only executing the necessary tasks is essential. However, at the same time you must be sure to do the task required for reliable operation in the next year. Doing not enough is too big of a risk.
This puts you in a difficult position as you have to decide on the basis of somewhat related and possibly inappropriate data which control valves to select for the next turnaround. At the same time, you are challenged to reduce spending so you must select the right control valves for your turnaround. The decisions you take, will have significant influence on the reliability of the process and number of unplanned of stops in the next months and years.
It would be ideal if you could determine, based on available data and actual usage and operating conditions, which control-valves to select for replacement or overhaul in your next turnaround.
Now your site may use HART diagnostics utilizing the HART diagnostic counters that are updated in your valve positioners and may indicate which control-valves require work. This requires Asset Management Software with the functions to fetch and record and analyse the diagnostic data from the positioners along with the associated HART pass-through analogue hardware needed to talk to and communicate with the positioner.
There is an alternative approach, using the data already available to control the valve and process. This is where the UReason Control Valve App comes in.
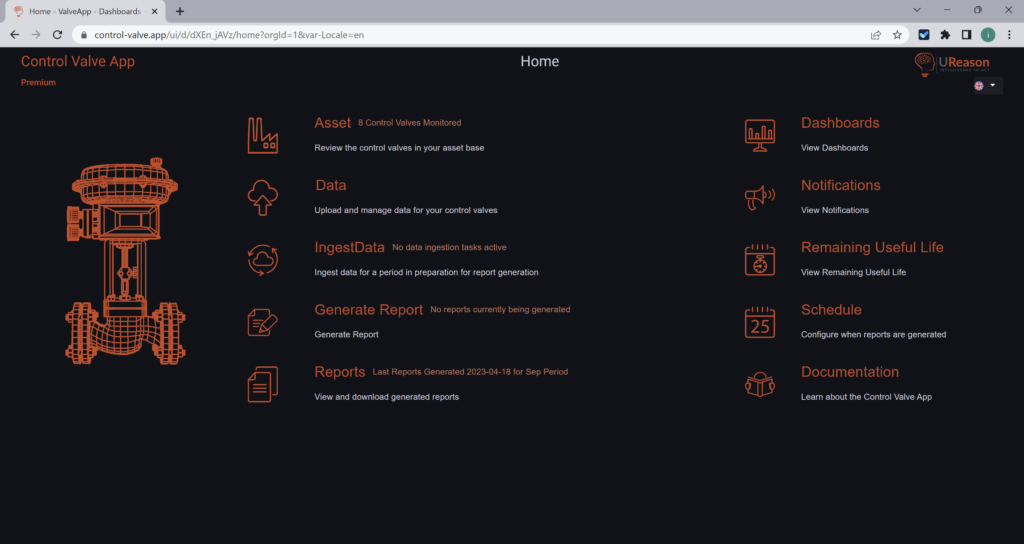
The app utilises the setpoint and position, or controlled variable information, to determine the operational performance of the control valve and provides insights in controller performance, valve and actuator issues. Valuable information on stiction, packing wear and rest of useful lifetime is determined by the app based on real usage and issues found. It does this using deterministic knowledge models, probabilistic risk models and combines this with different AI models. Next to the operational (process) data, which can be extremely valuable to identify maintenance tasks, the models need information about the valve and actuator such as installation date (recommissioning date) and performance metrics.
Based on the models the Control Valve App determines the Rest of Useful Lifetime of the actuator and the valve. This is presented to the user:
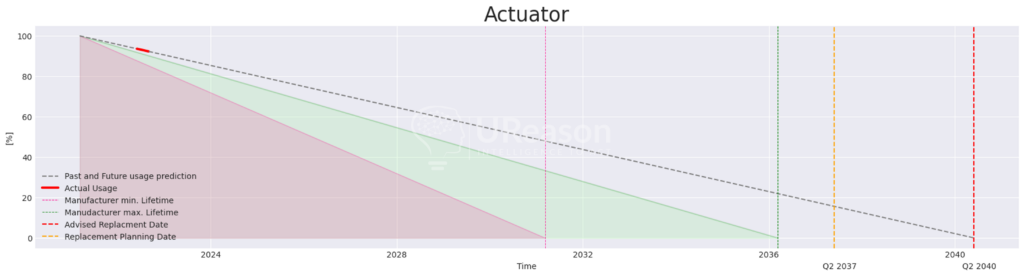
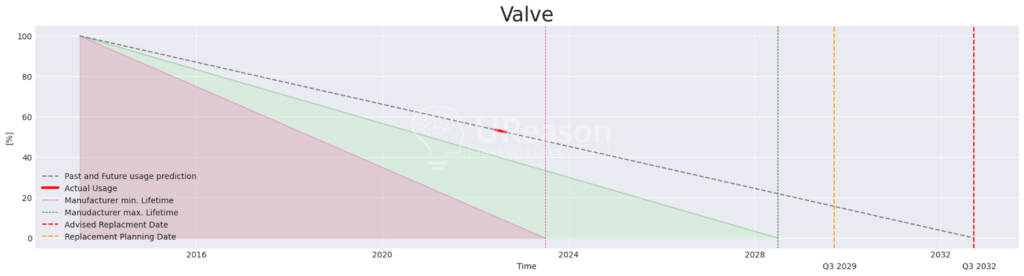
And can be easily used as basis to plan the required work during the next turnaround or it can be integrated with your CMMS system to schedule inspection or replacement.
At one of our customers the insights generated in RUL by the Control Valve App, for so called zero-maintenance valves and actuators, allowed them to generate a replacement plan that not only spreads the CAPEX needs for the replacement over multiple years but also the work required for these replacements. In summary replacing only the valves and actuators required to be replaced at the time when needed.
The Control Valve App is a pragmatic Industry 4.0 tool for a Reliability Engineer. It allows him to use the data from actual plant operation to assess the condition and RUL of the control valves. It is a “data driven” approach to understand the asset and component condition and plan accordingly.