Valves don’t only fail in the middle of the night. It just seems like they do. The ones that fail in the middle of the night are what detectives call “the usual suspects.” Process safety experts call them “bad actors” and they really are the stuff of nightmares.
Valve failures run from hardly noticeable to horrible catastrophies. The hardly noticeable ones, if you don’t catch them, can swiftly turn into a horrible catastrophy. The problem could be in the actuator; it could be in the trim; or it could be an improper signal from the valve controller; or it could be something entirely different that causes the valve to fail.
Sometimes, the valve failure is a puzzle. You can’t figure out what is failing. So, you keep replacing the trim, the valve stem, the actuator diaphragm or motor, and the valve works for a while but fails again much faster than it should. Usually in the middle of the night.
If you are like most process plants, you have a DCS vendor, a Safety system vendor, and a CMMS vendor. The responsibility for observing your valves is divided between the three vendors. In some cases, there is only one vendor providing all three services. These vendors, or the divisions of a single vendor, are not always in sync with operations and the need to figure out how to keep valves that are “bad actors” from failing catastrophically. With split responsibility, comes no accountability. What happens then is that valves are not always inspected, even though they should be. In addition, while some DCS/AMS vendors provide valve health services, they usually only do it for their own brands, and only for certain models.
Couple this with the loss of people during the COVID-19 pandemic and afterward, and there are not enough people to do the maintenance on the plant that should be done, let alone do the required partial-stroke-testing on safety instrumented valves, or inspection of control valves and their actuators to look for increased stiction or non-linearity or leakage.
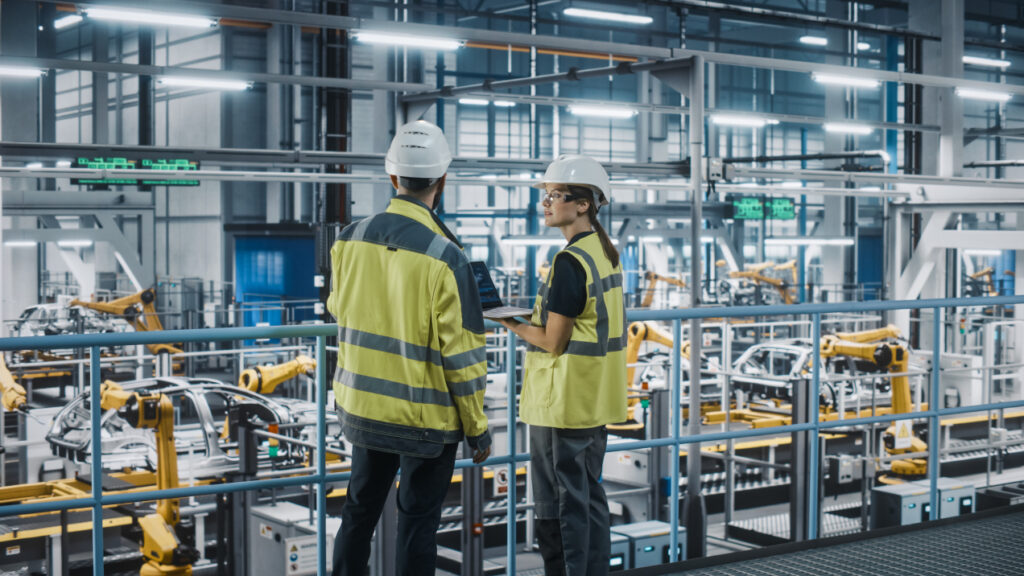
So here you are. You have a plant where the same set of control valves fails over and over. Just to set up to get the CMMS, the Safety Instrumented System, and the DCS to put out data so you can tell when those valves are getting ready to fail, seems like the mating of elephants—lots of stamping, bellowing, and a result in two years.
Concentrating on the “bad actors” can give you a huge boost toward higher productivity and fewer unexpected shutdowns. You already have all the data you need to figure this out. And you can use a simple app to do it. You need some simple data: setpoint and valve position data from the control valve controller, and if position feedback isn’t available, additional data on controlled measurement flow/level/pressure/temperature and environment is needed. No additional hardware or sensors are required, just what you’ve already got.
You can use UReason Control Valve App—a simple, stand-alone app that will take the data you already have, and use it in an AI-based analysis engine to tell you which control valves will fail soon and when they fail.
Control Valve App (CVA) is based on extensive expertise of UReason in valves, actuators, and the relevant processes. It uses intelligent models that combine domain knowledge and artificial intelligence (AI) to provide immediate detailed analysis of the process and recommendations for control valves. In the basic app, a PDF report is the output, while the premium version can have an online dashboard and provide job orders in the maintenance management system of the plant.
If you want to see how the CVA works, and how you can best use it, you can download the CVA brochure.